The laser drilling process is a thermophysical process of the interaction between laser and material. It is determined by the laser beam characteristics (including laser wavelength, pulse width, beam divergence angle, focus state, etc.) and many thermophysical properties of the material. Laser drilling machine is the earliest practical laser processing technology, and it is also one of the main application fields of laser processing.
Ceramics are a class of inorganic non-metallic materials made of natural or synthetic compounds through forming and high-temperature sintering. It is a functional material with high melting point, high hardness, high wear resistance, and oxidation resistance. It is characterized by high hardness, high rigidity, It has high strength, no plasticity, high thermal stability and high chemical stability. It is also a good insulator and is often used in military industry, aerospace, high-end PCB and other fields.
Ceramic materials are limited by technological conditions during the machining and forming process, and various holes, grooves, and edges cannot be accurately reserved for assembly. Because technicians have to take care of the characteristics of ceramic materials that are high in hardness, brittleness, and easy to break, Processing precision drilling of ceramics, especially small holes and micro-hole processing, forming processing, thread processing, etc. The processing technology requirements are very high, and the range of material machinability needs to be expanded to make it more widely used. The current technology of drilling ceramic materials mainly includes
mechanical processing,
ultrasonic processing,
laser processing and other methods. Today we mainly introduce the technology of laser processing.
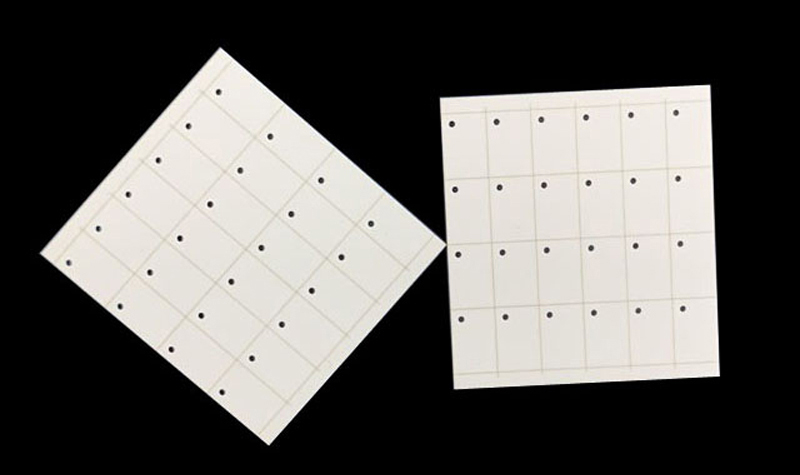
Lasers are also effective for processing small holes in superhard materials such as ceramics. Laser drilling generally uses pulsed lasers. The laser beam is focused on the ceramic workpiece through an optical system. The laser pulses with high energy density (106~109W/cm2) are used to melt, vaporize and evaporate the processed surface parts, thereby removing materials to achieve small Hole processing.
Advantages of laser drilling:
1) It belongs to non-contact processing, which will not cause mechanical extrusion or mechanical stress to the material, and is safe and reliable;
2) Simple operation, fast processing speed, high efficiency, and easy to realize mechanization with computer control;
3) High precision, low processing cost and high level of technology.
The laser focusing spot can converge to the order of wavelength and concentrate high energy in a small area. It is especially suitable for processing micro and deep holes. The minimum aperture is only a few microns, and the hole depth to aperture ratio can be greater than 50. Ceramic laser drilling is mainly used in ceramic body parts such as shell earpiece and antenna drilling, earphone drilling, etc. It has the advantages of high efficiency, low cost, small deformation, and wide application range.
As a flexible processing method, laser has demonstrated extraordinary capabilities in ceramic substrate processing technology. In addition to
ceramic laser cutting, scriding and perforation, it can also be used for ceramic stickers, printing, marking and other production processes, which greatly saves industrial energy consumption.